IDTechEx Finds Removing Rare-Earths Drives Demand for Copper in EV Motors
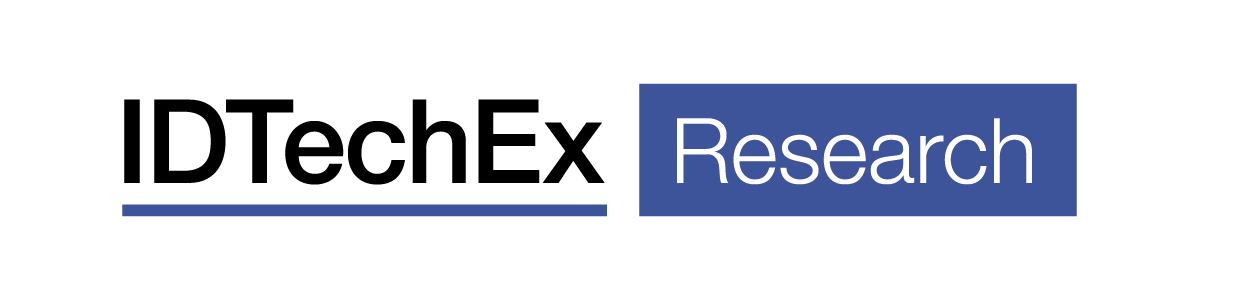
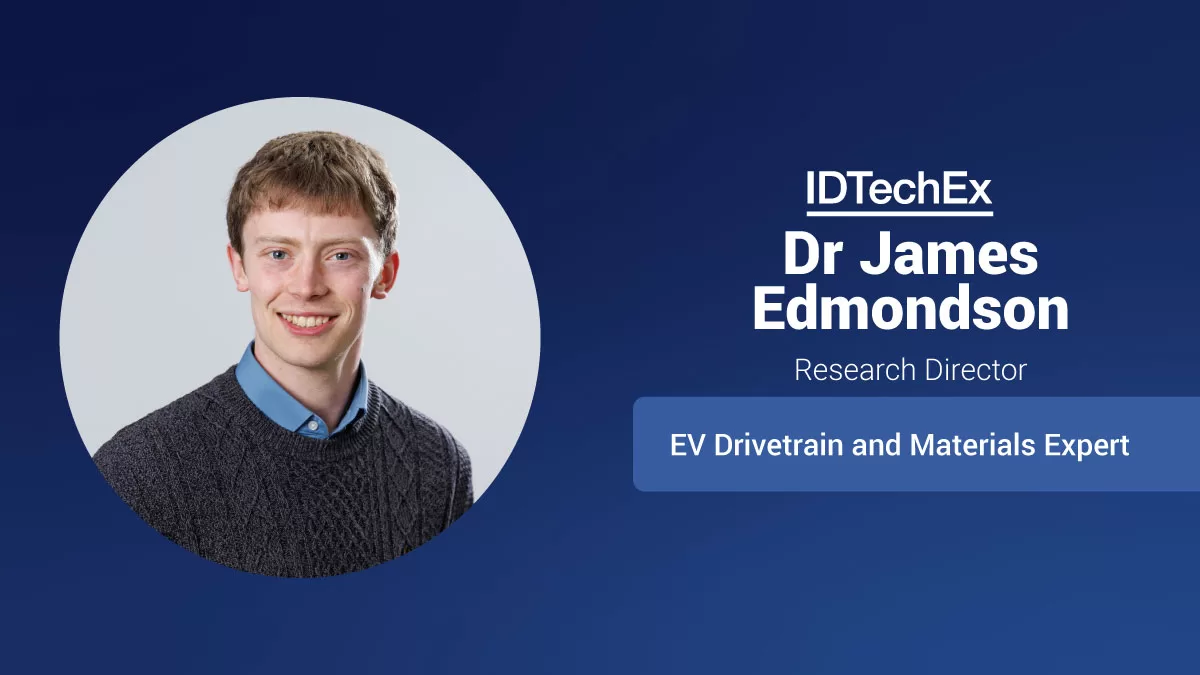
Author: Dr James Edmondson, Research Director at IDTechEx Electric motors are a core component of electrification in the automotive market. The market has heavily relied on rare earths for the permanent magnets used in these motors, but, as many will be aware, there is a drive to eliminate these rare earths due to their price volatility and environmental impact. Alternative motor technologies can often present a new and increased demand for copper. However, this trend can be offset somewhat by improvements to winding efficiency and copper utilization that have been seen in recent years. Regardless, the growing electrification of the automotive market will drive a 3.1-fold increase in copper demand for EV motors in 2034 compared with 2023. IDTechEx’s report on “Copper Demand for Cars 2024-2034: Trends, Utilization, Forecasts” analyses the key trends in the automotive market that will impact copper demand, including traditional components like the wiring harness and auxiliary electric motors and emerging technology like electrification components (batteries, motors, power electronics, high voltage cables), and autonomy (sensors and computing). The report considers technology evolution and provides forecasts within each of these components for copper demand between 2024 and 2034. Where is copper used? A motor consists of a stationary component (stator) and a rotating component (rotor). In general, the stator will consist of a steel stack with copper windings that are used to generate an electromagnetic field. The rotor materials vary depending on the technology. Permanent magnet motors include magnets in the rotor, induction motors include copper or aluminum bars, wound rotor motors include further copper windings, and reluctance motors are predominantly steel. Eliminating magnets increases copper Induction motors have moved from being a popular drive motor to being mostly reserved for secondary drive applications. Depending on whether they have a copper or aluminum rotor, they can increase the copper content of motors compared to permanent magnet options. The wound rotor motor is proving to be the go-to magnet-free option, and the use of copper windings on the rotor significantly increases the copper content of the motor, with some examples presenting more than double the copper of a comparable permanent magnet motor. There are alternative motor technologies that could keep copper similar to permanent magnet motors; for example, the reluctance motor’s rotor is predominantly steel and does not add copper or aluminum. However, these have traditionally had power density, acoustic noise, and efficiency challenges. There are several avenues for improvement here, with several players working on this type of design, but it is yet to be demonstrated in a mass-manufactured electric car. The more emerging axial flux motor presents very high power density and, therefore, on a copper content per kW of power basis, provides a much lower copper demand.
|
||
Relative copper content of electric motors used in electric cars. Source: IDTechEx |
||
Winding technology to reduce copper The above discussion relates to the rotor, but there are efforts to improve the copper utilization of windings in the stator. Traditionally, these windings are made of many individual small round wires wound together around the stator. In 2021, hairpin-type windings took a similar global market share in EVs to round wires and actually overtook round wires in 2022. Hairpin winding involves square/rectangular wires being used, increasing the fill factor of the slots, making better use of the space available, and reducing the amount of extra copper windings that are left hanging at either end of the motor. A higher fill factor can be used to increase the amount of copper mass per motor, or more effective filling can reduce the overall length (and hence copper content) of the motor for the same performance. The next stage of evolution involves having these hairpin windings pre-wound so that each bar does not need individually inserting and welding. This improves manufacturability, enables more stator poles, and further reduces the overhanging end windings. This process has been demonstrated by companies like Schaeffler, Lucid, and BorgWarner, which has a similar concept called “S-winding”. There is also potential for copper to be replaced by aluminum in the stator windings. Aluminum has an overall poorer volumetric performance, requiring a higher volume of aluminum for the same performance as copper. The motivation to substitute aluminum for copper is that aluminum is lighter and less costly than copper. Despite this, for the majority of applications, IDTechEx expects copper to remain as the primary stator winding material beyond some specific scenarios where volumetric motor performance is not as critical. Outlook for EV motor copper demand While there have been, and will continue to be, incremental improvements to the efficiency with which copper is applied within an electric motor, the rapidly growing EV market creates large new demands for copper in EV motors. This will be compounded somewhat with a greater share of magnet-free motor designs hitting the market with players like BMW and Renault utilizing wound rotor motors and tier 1 suppliers such as ZF, MAHLE, Vitesco, and others producing wound rotor designs. IDTechEx’s report “Copper Demand for Cars 2024-2034: Trends, Utilization, Forecasts” builds on its “Electric Motors for Electric Vehicles 2024-2034” report to provide an in-depth look at motor technology's impact on copper utilization, predicting a 3.1-fold increase in copper demand for EV motors between 2023 and 2034. The report also predicts that trends like electrification and autonomy will drive a 4.8% CAGR in copper demand until 2034 for the automotive market. To find out more about “Copper Demand for Cars 2024-2034: Trends, Utilization, Forecasts”, including downloadable sample pages, please visit www.IDTechEx.com/CopperForCars. Upcoming free-to-attend webinar Copper Utilisation Within Electric Powertrains Dr James Jeffs, Senior Technology Analyst at IDTechEx, will be presenting a free-to-attend webinar on the topic on Wednesday 24 January 2024 – Copper Utilisation Within Electric Powertrains. Key points covered in this webinar:
Click here to find out more and register your place on one of our three sessions. If you are unable to make the date, please register anyway to receive the links to the on-demand recording (available for a limited time) and webinar slides as soon as they are available. |